

generated in relation to amplitude and frequency of the dynamic motion. The piezoelectric accelerometer, the second important focus of this paper, consists of two parts: a piezoelectric material beam and a seismic mass.
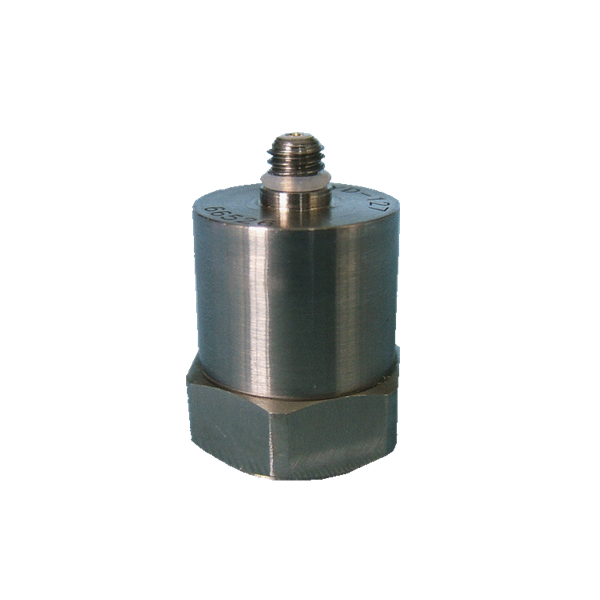
on a simple spring-mass principle in which strain is. In performance measurement, we obtain the charge sensitivity, natural frequency, working bandwidth and noise equivalent acceleration of 22.74 pC/g, 867.4 Hz, 10–200 Hz (within ±5% deviation) and 5.6 \(\mu \) as our design targets. All mechanical accelerometer designs are based. The piezoelectric accelerometer measures acceleration and this signal can be electronically integrated once to provide the velocity signal and a second time to. For the first time, we use aerosol deposition method to deposit thick PZT film during the fabrication process to achieve high sensitivity. Under acceleration, the seismic mass of the accelerometer. To figure out whether the design is suitable for SHM, working bandwidth and noise level are obtained via simulation. The most common AC-response accelerometers use piezoelectric elements for their sensing mechanism. They are simple to use and accurate over a wide frequency. It is a cantilever beam structure with a tip proof mass and PZT sensing layer. ICP accelerometers are designed to measure vibration and shock for a wide variety of applications. Potentially applied in low-noise applications such as structural health monitoring (SHM), a 1-axis piezoelectric MEMS accelerometer based on aerosol deposition is designed, fabricated, simulated, and measured in this study. integrated electronic accelerometers operate from 2 to 4 mA constant current, some operate from as little as 0.
